The Main Principles Of Alcast Company
Some Ideas on Alcast Company You Should Know
Table of ContentsThe Main Principles Of Alcast Company The 20-Second Trick For Alcast CompanyThe Main Principles Of Alcast Company Alcast Company Fundamentals ExplainedAlcast Company Things To Know Before You Get ThisA Biased View of Alcast CompanyThe smart Trick of Alcast Company That Nobody is Talking AboutExamine This Report about Alcast Company
It possessed good strength and machinability. There are lots of other aluminum alloys that can be utilized for casting parts. To find out which alloys would be excellent for your jobs, contact Impro.

Different elements and amounts create a wide array of desirable physical and chemical homes. And the Light weight aluminum Organization (AA), based in North America, has created requirements that control light weight aluminum alloys' structure, residential properties, and classification. There are 2 sorts of aluminum alloys functioned and cast. Factory employees develop these alloy types in different methods, which considerably influences their characteristics.
8 Easy Facts About Alcast Company Shown
Cast light weight aluminum alloys are made by melting pure aluminum and combining it with other steels while in liquid form. The mix is poured into a sand, pass away, or investment mold. After solidification, the metal is removed from its mold. At this stage, it is in either its final type or as a billet or ingot for further processing.

There are many minor differences between wrought and cast aluminum alloys, such as that actors alloys can contain extra substantial amounts of various other steels than functioned alloys. However the most noteworthy difference in between these alloys is the fabrication procedure via which they will most likely to supply the end product (aluminum foundry). Other than some surface therapies, cast alloys will certainly leave their mold in almost the specific strong type desired, whereas wrought alloys will undergo a number of adjustments while in their strong state
Little Known Questions About Alcast Company.
If you assume that a functioned alloy might be the ideal for your project, have a look at a few of our posts that explain even more concerning certain functioned alloys, such as Alloy 6061 and Alloy 6063. On the various other hand, if you think a cast alloy would be better for you, you can learn much more concerning some actors alloys in our Alloy 380 and Alloy 383 posts (coming quickly).
When selecting a light weight aluminum foundry for your production requirements, it's crucial to examine numerous factors. Among one of the most important aspects to think about is the experience and capability of the factory. Picking a shop that has the right expertise of the light weight aluminum spreading process, and the portfolio to show for it, assists to have an effective end result for your project.
See This Report about Alcast Company
Having the experience and industry knowledge to engineer your castings for optimum manufacturing and quality outcomes will streamline the project. Producing light weight aluminum castings requires a complex set of processes to accomplish the ideal outcomes. When choosing a brand-new light weight aluminum shop to companion with, ensure they have comprehensive industry experience and are well-informed regarding all aspects of the aluminum spreading procedure: style, production, material evaluation, and product screening.
The factory ought to also have a tried and tested track document of providing remarkable products that fulfill or surpass consumer assumptions. Quality control ought to also go to the top of your listing when selecting an aluminum shop. By working with a certified shop that follows the criteria for top quality control, you can safeguard the honesty of your product and ensure it satisfies your specifications.
The 8-Second Trick For Alcast Company
By selecting this website a firm that provides solutions that satisfy or surpass your item requirements, you can be certain that your task will be completed with the utmost precision and efficiency. Specific light weight aluminum shops concentrate on specific types of producing procedures or casting approaches. Various parts need different production methods to cast aluminum, such as sand spreading or pass away spreading.
Die casting is the name provided to the procedure of producing complicated metal components through use of mold and mildews of the element, likewise called dies. The process makes use of non-ferrous steels which do not consist of iron, such as light weight aluminum, zinc and magnesium, as a result of the preferable residential or commercial properties of the metals such as reduced weight, greater conductivity, non-magnetic conductivity and resistance to deterioration.
Pass away casting manufacturing is quick, making high manufacturing degrees of elements easy. It generates more parts than any type of other process, with a high level of precision and repeatability. For more information concerning die spreading and die casting materials made use of while doing so, kept reading. There are 3 sub-processes that drop under the group of die casting: gravity pass away casting (or irreversible mold and mildew casting), low-pressure die spreading and high-pressure die casting.
How Alcast Company can Save You Time, Stress, and Money.
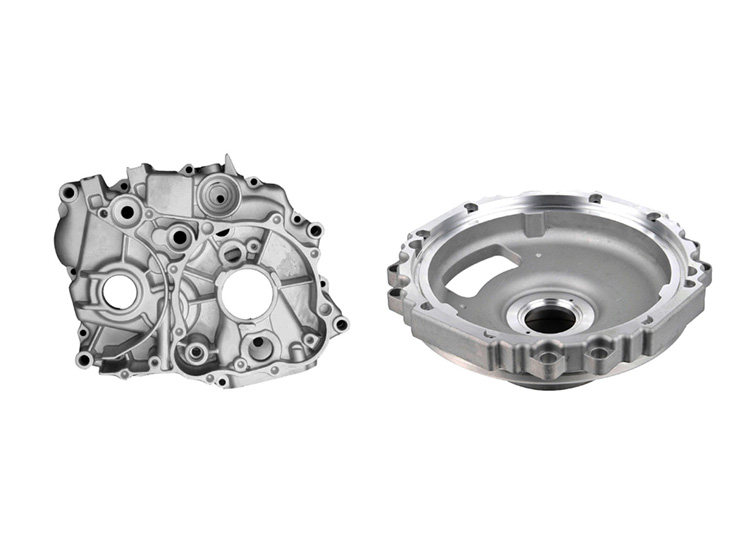
The pure metal, also referred to as ingot, is contributed to the heater and kept at the molten temperature level of the steel, which is after that transferred to the shot chamber and injected right into the die. The stress is after that maintained as the metal solidifies. As soon as the steel solidifies, the cooling process begins.
The thicker the wall surface of the component, the longer the cooling time because of the amount of indoor metal that also needs to cool. After the element is completely cooled down, the die cuts in half open and an ejection device presses the element out. Adhering to the ejection, the die is shut for the next shot cycle.
The Facts About Alcast Company Uncovered
The flash is the additional material that is cast during the process. This must be cut off making use of a trim device to leave simply the primary component. Deburring removes the smaller items, called burrs, after the cutting procedure. Lastly, the element is polished, or burnished, to offer it a smooth coating.
Nevertheless, this showed to be an incorrect test, because the tester can cut into an item and miss out on a location with porosity. Today, leading makers utilize x-ray screening to see the entire inside of elements without reducing into them. This allows them to a lot more accurately approve or turn down components. To reach the finished item, there are 3 key alloys utilized as die spreading material to select from: zinc, aluminum and magnesium.
Zinc is just one of the most previously owned alloys for die casting as a result of its lower expense of raw materials. It's additionally one of the stronger and secure metals. Plus, it has excellent electrical and thermal conductivity. Its rust resistance additionally allows the parts to be long-term, and it is just one of the much more castable alloys as a result of its lower melting factor.
Alcast Company - The Facts
As discussed, this alloy is among the most typically used, yet produces will, sometimes, pick light weight aluminum over zinc because of aluminum's production benefits. Light weight aluminum is extremely affordable and one of the extra versatile alloys. Light weight aluminum is made use of for a variety of different products and industries anything from window structures to aerospace products.